Projektstatus
Aktiv – 01.07.2021 bis 30.06.2024
Projektpartner
Fördermittelgeber: | Deutsche Forschungsgemeinschaft (DFG) |
|
|
Projektbeschreibung
Oxy-fuel combustion is a technology to capture and store CO2. This is achieved through combustion with pure oxygen instead of air. Replacing the nitrogen fraction of air with the much more chemically reactive and radiation-absorbing molecules CO2 and H2O leads to significant changes in the combustion process. Reaction rates, transport processes in the gas phase and the radiative heat transfer are altered fundamentally compared to combustion in air.
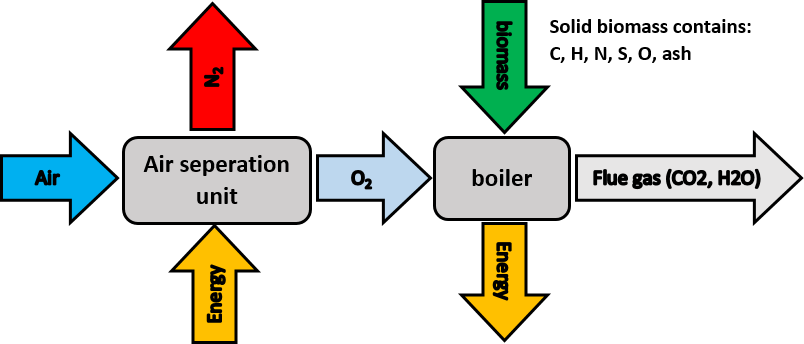
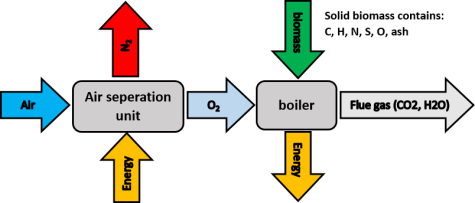
The project Oxyflame is divided into 21 subprojects with the overall objectives:
- Development of a comprehensive understanding of all relevant mechanisms involved in the combustion of solid, pulverised fuels in an oxy-fuel atmosphere
- Development of valid generalised models for combustion and transport phenomena in an oxy-fuel atmosphere, taking relevant effects on each scale into consideration
- Development of physics-based, efficient simulation methods for the layout of oxy-fuel combustion chambers, to allow for model-based design
Subproject C7
The relevance of various phenomena (such as turbulence, chemical kinetics, or radiation) on the overall structure and stability of a flame is affected by the scale and boundary conditions of the furnace. For instance, radiative heat loss from the flame increases with the size of the enclosure if the walls are cooled, which may lead to local flame extinction and formation of emissions, such as soot, hydrocarbons, and CO.
The main objective of this subproject is to identify the effect and interaction of these phenomena in a furnace operating at conditions close to industrial applications, in particular, the mechanisms leading to pollutant formation caused by flame instabilities. This subproject will evaluate the influence of scale on the flame structure, which will allow assessing to what extent the results of project partners (determined on a smaller scale) can be transferred to furnaces on an industrial scale. The experiments are conducted in a water-cooled top-fired furnace with thermal power of 1 MWth. Using a variety of complementary measurement technologies at various ports along the furnace axis, mean values, fluctuations, temperature, gas composition, and radiative heat transfer are determined in collaboration with project partners.
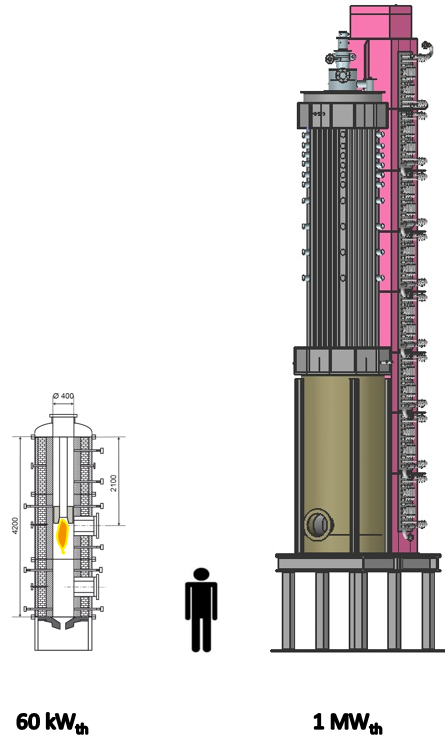